圧子/ドレッサの参考情報
圧子について
圧子について
圧子の一般的な使われ方は、硬度計と呼ばれる硬さ試験機に取り付けられ、荷重をかけて試験材料に押し込み、できた圧痕の深さや面積により試験材料の硬さが判定されます。硬さを計測するのは非常に難しく、計測器ではなく試験機と呼ばれるのもその所以です。
圧子の先端には、ダイヤモンドや鋼球などが使われ、硬い材料や薄い物の試験にはダイヤモンド圧子が使われます。
日本初のダイヤモンド圧子は、ロックウェル硬さ試験機用を1933年に当社が完成させました。
右の図は、ビッカース硬さ試験機用ダイヤモンド圧子の各部の名称です。
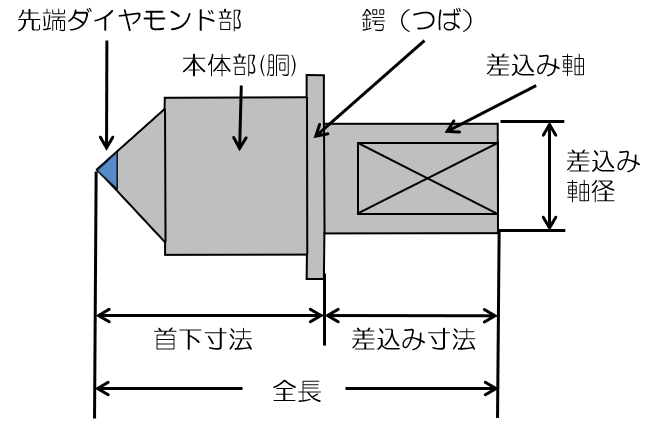
硬さ試験方法と圧子の種類
硬さ試験方法と圧子の種類
試験方法 | 分類 | 記号 | 試験材料 | 圧子形状 | 硬さ算出法 |
---|---|---|---|---|---|
ロックウェル | 押込み | HR | 金属、硬質プラスチック等 | 頂角120° 円錐 または鋼球 |
試験荷重を加えた後、基準荷重に戻したときのくぼみの深さの差 |
ビッカース | 押込み | HV | 金属、セラミックス、 プラスチック等 |
頂角136° 正四角錐 | 圧痕の対角線の長さから計算される表面積 |
ヌープ | 押込み | HK | 金属、セラミックス、 プラスチック等 |
頂角172.5° 菱形の四角錐 | 圧痕の投影面積 |
ショア | 反発 | HS | 金属等 | 先端に半球状のダイヤモンドを埋め込んだハンマー | ハンマーを落とした時の跳ね返り高さ |
ロックウェル硬さ(HR)・ロックウェル圧子
ロックウェル硬さ試験は、最初に基準荷重(初試験力)で圧子を試験材料に押し込む事により、材料表面の酸化膜や凹凸をある程度無視出来る点が特徴です。
基準荷重をかけた後、試験荷重(全試験力)でさらに押し込み、試験荷重から基準荷重に戻す。試験荷重によって得られたくぼみのうち、弾性回復後に残った塑性変形深さが得られ、最初の基準荷重によって得られた深さとの差がその材料の硬さ値となります。
基準荷重10Kgfをロックウェル硬さ、基準荷重3Kgfをロックウェルスーパーフィシャル硬さと呼ぶ。
ロックッウェル硬さは、深さ2μmが1硬さ、ロックウェルスーパーフィシャル硬さは1μmが1硬さとなる。
HR+スケール記号で表記します。
ロックウェル圧子(ダイヤモンド)は、先端が120° 0.2Rの円錐で、Cスケール(荷重150㎏)、Aスケール(荷重60㎏)と、スーパーフィシャル用がある。
形状が同じでもRの先端精度などにより硬さに大きな影響が出るため、 Aスケールとスーパーフィシャル用は、 Cスケールよりも高い精度の追い込みを行い、硬さを調整している。
スケールについて
スケールとは、測定に用いる圧子の種類、基準荷重、試験荷重が規定された試験条件のこと。
ロックウェル硬さ試験には、ダイヤモンド圧子の他に直径の大きさにより4つの鋼球圧子がある。
また、試験機の荷重装置は6種の荷重が選択出来き、5種類の圧子と6種類の試験荷重(全試験力)の組み合わせで30種類のスケールと呼ばれる試験条件がある。
30種類の内、基準荷重(初試験力)が10Kgfの15種類のスケールをロックウェル硬さ、 基準荷重が3Kgfの15種類のスケールをロックウェルスーパーフィシャル硬さと呼び、慣例的に試験材料ごとに適用スケールは決まっている。
ダイヤモンド圧子は、ロックウェル硬さのA、D、Cスケール、スーパーフィシャル硬さの15N、30N、45Nスケールの合計6つのスケールで使用することになている。
ビッカース硬さ(HV)・ビッカース圧子
正四角錐のダイヤモンド圧子を押し込み、圧痕の対角線の長さから表面積を計算し、その面積を硬さとする。
圧痕が小さく、小さな物や薄い物の測定が可能。焼き入れの深さ等の硬さ分布測定に適している。
ビッカース圧子は、先端ダイヤが対面角136°±30′の正四角錘で、マイクロビッカースも形状は同じ。
また、マイクロビッカースでも測定出来ない、薄膜などの硬さ、ヤング率、ナノレベルの圧痕を測定するために、三角錘圧子(バーコビッチ圧子、ベルコビッチ圧子、またはナノインデンター用圧子、超微小硬度計用圧子とも呼ばれる)が使用されます。
ビッカース圧子の圧痕
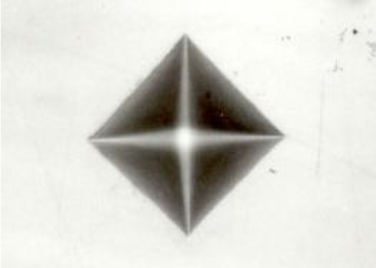
三角錐圧子の圧痕
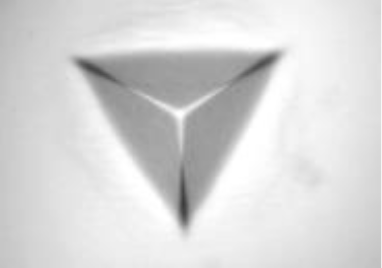
ヌープ硬さ(HK)・ヌープ圧子
押し込み硬さの一つ。菱形のダイヤモンド圧子を押し込み、圧痕の投影面積を硬さとする。ビッカース圧子より圧痕の深さが浅く、圧子の侵入深さも浅いため、薄物、表面膜の測定、ガラス等深く侵入するとチッピングを起こし測定しづらい物に適している。
ヌープ圧子は、対稜角が172°05′と130°の菱形の四角錘面を持っている。
ヌープ圧子の圧痕
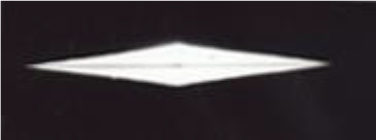
ショア硬さ(HS)・ショアハンマー
反発硬さの一つ。先端に半球状のダイヤモンドを埋め込んだ鋼のハンマーを一定の高さから落とし、跳ね返りの高さを硬さの値としている。目測で読み取るC型試験機と、ダイヤルゲージで読み取るD型試験機がある。
試験機が小型・軽量で、持ち運びができるD型は、大きな部品や圧延ロール、鉄道レールなどの大型製品をそのまま現場で測定可能。
ショアC型試験機用のCハンマーと、ショアD型試験機用のDハンマーを基本に、様々なハンマーを製作しています。
ブリネル硬さ
鋼球や超硬合金球の圧子で荷重をかけ、その荷重をくぼみの表面積で割った値が硬さとなる。
他の硬さ試験に比べくぼみが大きいので、試験材料の平均的な硬さを測定することが可能なため、硬さが均一ではない材料に適しています。
ドレッサについてと種類
ドレッサについてと種類
ダイヤモンド ドレッサについて
ダイヤモンドドレッサは、一般砥石やダイヤモンド・CBNホイールの目つぶれ、目づまり、外周振れを修正し良好な切れ味を回復させるための加工(ツルーイング・ドレッシング)や、成型(フォーミング)に使用するダイヤモンド工具。
ダイヤモンド フォーミングドレッサ
ダイヤモンドフォーミングドレッサは、先端のダイヤモンドを屋根形や楔形に研磨加工したもの。
ダイヤモンドの部分は研磨成形されており、衝撃に対して非常に弱い。治具に傾いて取付けられた場合には、ダイヤモンドに衝撃が加わり破損の恐れがあるため、正しく取り付ける必要がある。
使用時の切り込み量は、なるべく0.02mm以内にし、送り速度は表面粗さとの関係もあるが、250mm/min以内ならダイヤモンドの破損の危険は下がる。
使用時は必ず冷却水をかけること。特に倣い加工では成形距離が長いために発熱し易く、ダイヤモンドの摩耗を早めて寿命が短くなる。
アンギュラー研削、段付け円筒研削、ネジ研削、歯車研などで使用。
単石ダイヤモンドドレッサ
単石ダイヤモンドドレッサは、先端にエッジを突出させたダイヤモンドの原石を使用したもの。
ドレッサ用ダイヤモンドの大きさの目安は、ドレッシングされる研削砥石の砥石仕様(砥粒、粒度、結合度、結合剤)と、砥石寸法(直径、幅)から決まる。
使用時の切り込み量は、仕上げドレッシングでは0.015mm以下、粗ドレッシングでも0.04mm以下として、一度に大きく切り込むことはできるだけ避ける。
砥石の径・幅とダイヤモンドの大きさの目安
砥石の径 (mm) |
砥石の幅 (mm) |
ダイヤモンドの 大きさ |
---|---|---|
Φ150 > | 25 > | 1/3 ~ 1/4 ct |
Φ150 ~ Φ300 | 25 | 3/4 ~ 1 ct |
Φ300 ~ Φ450 | 25 ~ 40 | 1 ~ 1.5 ct |
Φ450 ~ Φ600 | 50 ~ 100 | 1.75 ~ 2 ct |
Φ600 < | 2 ct < |
多石ダイヤモンド ドレッサ
多石ダイヤモンドドレッサは、複数のダイヤモンドを固定したもの。
表面の1層に2個以上のダイヤモンドを等間隔に並べ埋め込んだタイプを単層多石ドレッサ、その層を積層させたタイプを多層多石ドレッサという。
単石ドレッサに比べ、1つのダイヤモンドにかかる負荷を低減できるため、長持ちする。
ダイヤモンド インプリドレッサ
ダイヤモンドインプリドレッサは、ダイヤモンド砥粒と耐摩耗性の高い金属粉末とを混合し焼結して、任意の形状や寸法で固めたチップをシャンクに取り付けたもの。
多くのダイヤモンド砥粒にドレス時の抵抗が分散され、ドレッサ摩耗の抑制と安定したドレスを実現。
種類は、シャンク形状、ダイヤモンド砥粒の粒度、チップ形状で区分されます。
インプリドレッサの仕様表示
インプリドレッサの仕様表示
2B4A7の例
-
2
ダイヤ部
寸法 -
B
ダイヤ部
形状 -
4
粒度
-
A
軸形状
-
7
挿込軸径
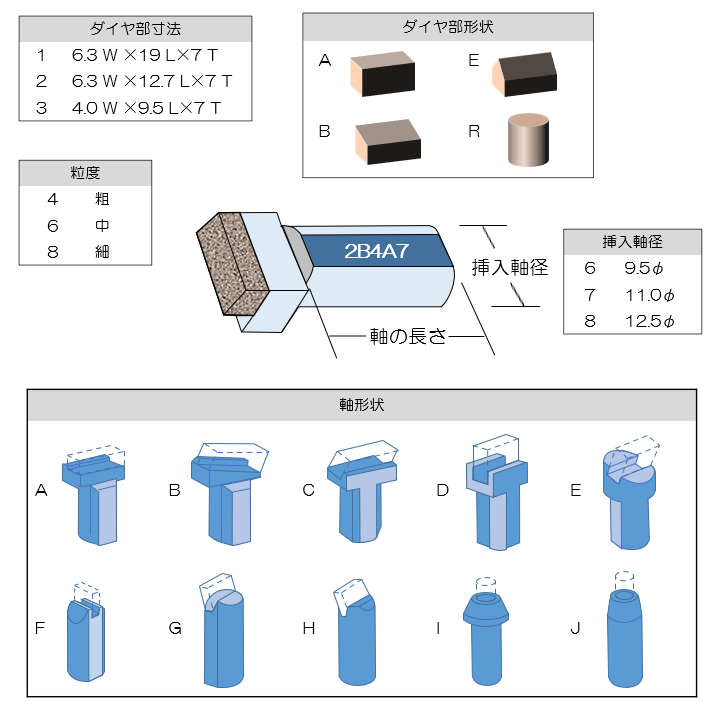