ダイヤモンド・cBNについて
ダイヤモンド・cBNについて
ダイヤモンドは、炭素からなる鉱物で、天然で最も硬い物質です。漢字では金剛石(こんごうせき)と表記されます。
量の単位は、宝石の重さを表す「カラット(carat)」で表され、1カラット(ct)は0.2グラムです。
20世紀後半に人工ダイヤモンドが製造され、現在工業用に使われるダイヤモンドの多くが人工です。
当社では、天然、人工それぞれの特徴を活かしたダイヤモンド工具のご提供をしております。
ダイヤモンドは、金属材料、特に鉄系の機械加工では構成元素である炭素と材料中の鉄組織にダイヤモンドの炭素が拡散浸透してしまい、硬いはずのダイヤモンドが意外に早く摩耗してしまいます。
よって、ダイヤモンド工具は、鉄系の材料の加工には向きません。
ダイヤモンドの次に硬い物質は、cBN(立方晶窒化ホウ素(cubic boron nitride)の頭文字、製品名などでは「CBN」と表記しています)という自然には存在しない化合物です。
常温時の硬さはダイヤモンドに劣りますが、炭素を含まないため、鉄系材料の加工に向いています。
加工材料によりダイヤモンドとcBNを使い分けることで、それぞれの特長を活かした加工が実現できます。
研削加工・研削工具について
研削加工・研削工具について
研削加工について
研削加工は、砥粒と結合剤などで構成された砥石(ホイール)を高速に回転させることで、ランダムに並んだ砥粒一つ一つが切れ刃の役割を持ち、被削材の表面をごくわずかづつ削り取る除去加工の一つです。
砥粒にダイヤモンドまたはcBNを使用する研削工具は、超砥粒ホイールと呼ばれます。
たくさんの硬く細かな刃で加工を行うため、硬い素材の高品位な加工を実現します。
研削する過程で、一般的には、砥粒が摩耗・脱落(自生発刃効果の場合もある)したり、切粉(被削材の削りくづ)が排出されます。
研削液は、加工で生じる熱を取り除き冷却する、砥石と被削材の潤滑性を高めることで熱の発生を抑える、切粉の排出を促す、等の効果があります。
研削加工と砥石の構造例のイメージ
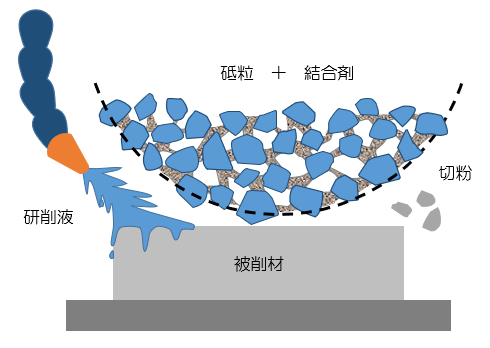
研削工具の種類
研削工具には、砥粒層の作用面の位置により、ストレートホイール(砥粒層の作用面が外周)やカップホイール(作用面が端面)があります。
その他、形状や用途により、以下のような種類があります。
・ストレートタイプ:センタレスホイール(センタレス用の機械で使用)、Vフェースホイール(砥粒層がV型形状をなすもの)、マルチホイール(ホイールを数枚重ねて使用するもの)、ネジ研ホイール(センタレス用の機械に使うホイールの外周にネジ加工をしたもの)、芯取りホイール(レンズ等の芯取り加工に使用されるもの)、玉摺ホイール(レンズ等の粗加工に使用されるもの)
・カップタイプ:6A7Sホイール(チップやペレットを付けたホイール)、両頭ホイール(ダブルディスク用グラインダーに使用される2枚1組のもの)
・異形ホイール(砥粒層がR付や溝付等、特殊な形状をしたもの):面取りホイール(半導体ウェーハや薄板ガラス等の面取りに使用)、ノッチホイール(半導体ウェーハのノッチ加工に使用)、他
・切断・溝入れホイール:リムソー、セグメントソー、マルチソー、スライシングソー
・その他:小径ホイール、コアドリル
研削加工の種類
研削加工の種類
-
円筒研削(円研)
円筒研削盤や万能研削盤を使用し、回転する砥石で円筒形の被削材の外周を削る加工。
砥石が被削材に対して動く方向によって、プランジ研削(砥石あるいは被削材を砥石半径方向へ移動させながら加工)と、トラバース研削(砥石を被削材の軸方向に平行移動させながら加工)に分かれる。また、砥石の回転方向と被削材の移動方向の関係で、アップカットとダウンカットに分かれる。
アップカット:砥石の回転方向と被削材の移動方向が同じになる研削方法。砥石と被削材の接触面積が大きく能率的な加工が行えるが、砥石にかかる負担が大きくなり、研削抵抗も大きくなるため、摩耗や損耗も比較的大きくなる。切粉を外側に排出しながら、下から上にすくい上げるように加工する方法。
ダウンカット:砥石の回転方向と被削材の移動方向が逆になる研削方法。砥石が被削材を削り取る時に、切粉を内側に巻き込みながら材料を掘り下げるように移動。 -
内面研削(内研)
内面研削盤を使用し、回転する砥石で円筒形の被削材の内面を削る加工。
被削材を回転させ、砥石に回転と送りを加えながら加工する工作物回転形方式と、被削材を固定して、砥石を自転と公転させながら送りを加え加工するプラネタリ形方式がある。
プラネタリ形方式は、重量物や形の複雑な被削材の加工に向いている。
円筒研削と同様に、トラバース研削とプランジ研削があります。 -
心なし研削(センタレス研削)
心なし研削盤(センタレス研削盤)を使用。被削材にセンター穴を開けず、固定したブレード(支持刃)、研削砥石と回転する調整砥石の3点で、回転する円筒形の被削材の外周を削る加工。
被削材をチャックなどで保持・固定しないため、取り付けや取り外し工程が発生せず、その分生産性が高くなります。スルーフィード研削(通し送り研削)は、砥石と調整砥石を一定の間隔にし、この間に被削材を通す研削方法で、量産加工に適している。少し傾けた調整砥石で、回転した被削材が軸方向に送られます。
その他にインフィード研削(停止研削)、エンドフィード研削、タンジェンシャル研削等があります。 -
平面研削(平研)
平面研削盤を用い、テーブルに固定した被削材を高速回転する砥石に押し当てることで、表面を少しずつ加工します。被削材の厚さを整えたり、平面度を高める時などに行われます。
砥石の軸の向き(縦軸/横軸)とテーブル形状(角テーブル/円テーブル)の組み合わせなどにより様々な研削方法が存在します。プロファイル研削(倣い研削、投影研削)
製品の形状を拡大してチャートと呼ばれる投影図を描き、投影機に光学的に映し出し、加工物とチャートを重ね合わせ、チャートからはみ出した部分を除去してゆく加工。
高い精度を必要とするテーバ、溝幅、溝深さ、凸R、凹Rなどの加工を行う。 -
歯車研削(歯研)
歯車研磨盤を用い、ギヤ等の歯面部分を研削し成型していく加工。
ネジ研削
ネジ研削盤を使用して、ねじ山の成形を行う加工
-
工具研削
加工する工具の種類により特定の研削盤を使う加工で、次のような工具研削盤がある。
ドリル研削盤、ホブ研削盤、正面スライス研削盤、超硬バイト研削盤、ブローチ研削盤、シェービングカッタ研削盤、鋸刃研削盤。
ホイールの仕様表示
ホイールの仕様表示
仕様表示例
-
SDC
砥粒の種類
-
200
砥粒の粒度
-
N
結合度
-
100
集中度
-
BDH
ボンドの種類
-
3.0
砥粒層の厚み(mm)
砥粒の種類
表示記号 | 砥粒の種類 |
---|---|
D | 天然ダイヤモンド |
SD | 人造ダイヤモンド(合成ダイヤモンド) |
SDC | 金属被覆合成ダイヤモンド |
BN(cBN) | 立方晶窒化ホウ素 |
BNC(CBNC) | 金属被覆立方晶窒化ホウ素 |
ダイヤモンド・cBN選択の目安
砥粒 | 加工素材 |
---|---|
ダイヤモンド | ガラス、セラミックス、シリコン、フェライト、超硬合金、水晶、石材、アルミなど非鉄系の硬質脆性材料 |
cBN | ニッケル合金、耐熱合金、焼き入れ鋼などの鉄鋼系材料 |
砥粒の粒度
粒度クラス | 粒度表示 | メッシュ | 平均粒径※(μm) |
---|---|---|---|
メッシュサイズ | 60 | #60/#80 | 250 |
80 | #80/#100 | 177 | |
100 | #100/#120 | 149 | |
120 | #120/#140 | 125 | |
140 | #140/#170 | 105 | |
170 | #170/#200 | 88 | |
200 | #200/#230 | 74 | |
230 | #230/#270 | 62 | |
270 | #270/#325 | 53 | |
325 | #325/#400 | 44 | |
ミクロンサイズ | 400 | 37 | |
600 | 30 | ||
800 | 20 | ||
1000 | 15 | ||
1200 | 13 | ||
1500 | 10 | ||
2000 | 8 |
※平均粒径(目安)の求め方: D(平均粒径μm)=15000/(粒径)
結合度
表示 | ボンドの硬さ |
---|---|
A | 柔らかい |
~ | |
N | 標準 |
~ | |
Z | 硬い |
集中度
表示 | 砥粒の体積含有率(vol%) |
---|---|
200 | 50.0% |
175 | 43.8% |
150 | 37.5% |
125 | 31.3% |
100 | 25.0% |
75 | 18.8% |
50 | 12.5% |
体積含有率25%(vol%)を集中度100と設定(ダイヤモンドの場合、約4.4ct/㎝³ ※1ct(カラット)=0.2g)。
ボンドの種類・特徴
ボンドの種類・特徴
-
メタルボンド
・金属粉とともに厳格な温度・雰囲気管理のもとで粉体焼結するボンド
・放熱性に優れ、砥粒の保持力が高く、耐摩耗性に優れる
・独自の加工技術により高精度な形状成形を実現する総形ホイールの製作が可能であり、形状の保持力も高い -
レジンボンド
・熱硬化性樹脂を主成分とし、様々な充填剤により幅広い要望に対応するボンド
・切れ味に優れ、鏡面など高品位加工が可能
・複雑な形状の総形ホイールの製作も可能 -
ビトリファイドボンド
・ガラス質の無機材料を用いたボンドで有気孔と無気孔のタイプがある
・硬くて脆い性質を活かして、高負荷の条件で切れ味、自生発刃性に優れる
・砥粒の集中度や気孔率のコントロール等アレンジ性が高い -
電着
・独自のメッキ法により砥粒をニッケルメッキで固着する
・焼結ボンド系ホイールに比較して砥粒密度が圧倒的に高い
・砥粒の突出し量の操作が可能で、切れ味が良く効率的な研削を実現
・砥粒の保持力が強く脱落が少ない
・様々な形の台金に対応した総形ホイールの製作が可能 -
ボンド選択の目安
ホイールの形状表示
ホイールの形状表示
-
形状表示例(6A2Cの場合)
-
台金の基本形状
-
砥粒層の断面形状
-
砥粒層の位置
-
モディフィケーション
-
タイプ別ホイールの主な形状表示(カップタイプ)
表示 形状 6A2 プレンカップ
6A9 プレンカップ(外周)
9A3 両面カップ
4A2 ディッシュ
4C9 ディッシュ
11A2 フレアカップ
11V9 プレンカップ(外周角度付)
11C9 フレアカップ(L字型)
表示 形状 11Y9 フレアカップ(L字角度付)
11B2 フレアカップ(角度付)
12A2 ディッシュ
12V9 ディッシュ(外周角度付)
12C9 ディッシュ(L字型)
12V4 ディッシュ(内側に傾斜付)
12V5 ディッシュ(外側に傾斜付)
-
タイプ別ホイールの主な形状表示(ストレートタイプ)
表示 形状 1A1 ストレート
3A1 ストレート(片ボス付)
14A1 ストレート(両ボス付)
6A1 ストレート
9U1 ストレート(コの字型)
1L1 両角R付ストレート
表示 形状 1FF1 R付ストレート
1F1 R付ストレート
1V1 角度付ストレート
1B1 角度付ストレート
1EE1 Vフェイス
1E1 Vフェイス
ツルーイング・ドレッシング
ツルーイング・ドレッシング
ツルーイング・ドレッシングとは
ツルーイング(形直し)とは、ホイール使用面の振れ取りと形状の修正作業。ドレッシング(目立て)とは、目づまり及び目つぶれした砥石面を排除し、新しい鋭い切れ刃を出したり、その新しい刃の突き出し量を調整したりする作業で、研削加工を効果的に行うためには欠かせない。
目詰まり、目つぶれ、目こぼれ等、工具の状況に合ったツルーイング・ドレッシング方法と被削材の加工精度に合ったドレッシング条件を選択する必要があります。