Basic information about indenter & dressers
About indenters
In the common use of indenters, the indenter is attached to a hardness testing machine called a hardness tester, and then a load is applied to press it into the test material. The hardness of the test material is determined by the depth or area of the indentation. It is very difficult to measure hardness, which is why it is called a testing machine instead of a measuring instrument.
The tip of the indenter is made of diamond or steel balls, and diamond indenters are used for testing hard materials and thin objects.
Japan's first diamond indenter for Rockwell hardness testers was developed by our company in 1933.
The figure on the right shows the names of the parts of the diamond indenter for the Vickers hardness tester.
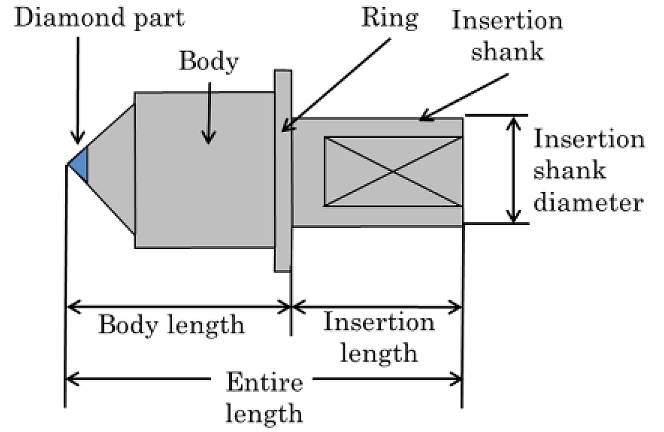
Types of hardness testings & indenters
& indenters
Type of hardness testing |
Method | Symbol | Testing materials |
Indenter shape | Hardness determination method |
---|---|---|---|---|---|
Rockwell | Indentation | HR | Metal, Hard plastic, etc. |
120° Conical tip or steel ball |
Difference between the depth remaining after the test load and the depth obtained by the reference load |
Vickers | Indentation | HV | Metal, Ceramics, Plastic, etc. |
136° Square pyramid tip | Surface area of the indentation calculated from the length of the diagonal line |
Knoop | Indentation | HK | Metal, Ceramics, Plastic, etc. |
172.5° Rhombic square pyramid tip |
Projected area of the indentation |
Shore | Rebound | HS | Metal, etc. | Steel hammer with a hemispherical diamond embedded in the tip |
Hight of the rebound after a hammer is dropped |
Rockwell hardness (HR), Rockwell indenter
The Rockwell hardness test is characterized by the fact that the indenter is first pressed into the test material with a reference load (initial test force), which makes it possible to ignore the oxide film and unevenness of the material surface to some extent.
After the reference load is applied, the material is further pressed under the test load (full test force) and then returned from the test load to the reference load. Of the indentation obtained by the test load, the plastic deformation depth remaining after elastic recovery is obtained, and the difference from the depth obtained by the initial reference load is the hardness value of the material.
The hardness measured with the reference load of 10 kgf is called Rockwell hardness and that with the reference load of 3 kgf is called Rockwell superficial hardness.
The Rockwell hardness is defined as 1 when 2 μm depth is obtained and the Rockwell superficial hardness as 1 when 1 μm depth is obtained. The Rockwell hardness is denoted by the HR + scale symbol.
A Rockwell diamond indenter with 120° and a 0.2R conical tip is available in C scale (150 kg test load) and A scale (60 kg test load), and also includes the one for superficial hardness. Even if the shape is the same, the hardness is greatly affected by the round tip's accuracy and shape. Therefore, the hardness obtained by the A scale and superficial indenters is adjusted through higher accuracy processing than that used for the C scale indenter.
Scale
Scale is a test condition in which the type of indenter, reference load, and test load used for measurement are specified. In addition to the diamond indenter, there are four other types of steel ball indenters for Rockwell hardness testing, depending on their diameter.
In addition, for the loading device of the testing machine, one can select 6 different loads, and there are 30 different test conditions, called scales, in combination with 5 different indenters and 6 different test loads.
When, of the 30 scales, 15 scales with a reference load of 10 kgf are used to obtain hardness, it is called Rockwell hardness. Hardness obtained by 15 scales with a reference load of 3 kgf is called Rockwell superficial hardness. The applicable scale is conventionally determined for each test material.
Diamond indenters are to be used in a total of 6 scales: A, D, and C scales for Rockwell hardness, and 15N, 30N, and 45N scales for superficial hardness.
Vickers hardness (HV), Vickers indenter
A square pyramidal diamond indenter is pressed in and the surface area is calculated from the length of the diagonal line. Hardness is defined by this calculated area. Since the indentation is small, small or thin objects can be measured. It is suitable for measuring hardness distribution such as the depth of quenching.
The Vickers indenter has a square pyramid shape with a face angle of 136°±30′ of the tip diamond, and the micro-Vickers has the same shape.
Triangular pyramid indenters (also called Berkovich indenters or nanoindenters, or indenters for ultramicro hardness testing) are used to measure the hardness of thin films, Young's modulus, and nano-size indentation that cannot be measured with micro-Vickers.
Indentation of Vickers
indenter
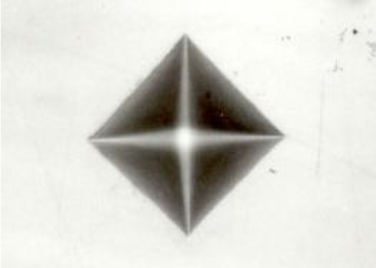
Indentation of
triangular pyramidal
indenter
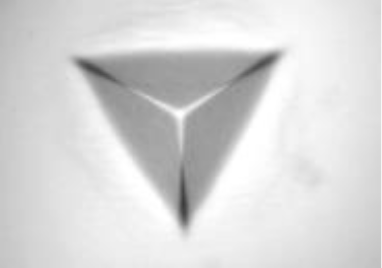
Knoop hardness (HK), Knoop indenter
This is one of the indentation hardness. A diamond indenter with a rhombic shape is pressed in and the projected area of the indentation is used as the hardness. Since the indentation depth is shallower than that of a Vickers indenter and the indenter's penetration depth is also shallower, it is suitable for measuring thin objects, surface films, and objects such as glass that are difficult to measure due to chipping if penetrated deeply.
The Knoop indenter has rhombic square pyramid faces with dihedral angles of 172°05′ and 130°.
Indentation of Knoop indenter
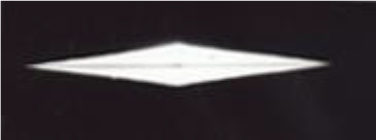
Shore hardness (HS), Shore hammer
This is one of the rebound hardness. A steel hammer with a hemispherical diamond embedded in the tip is dropped from a certain height, and the height of the rebound is used as the hardness value. There are two types of testers: the C-type tester, which takes readings by the naked eye, and the D-type tester, which takes readings with a dial gauge. The D-type tester is compact, lightweight, and portable, and can be used to measure large parts, rolling rolls, railroad rails, and other large products directly on site.
We manufacture a variety of hammers based on C hammers for Shore C-type testers and D hammers for Shore D-type testers.
Brinell hardness
A load is applied with an indenter of steel or cemented carbide balls, and the hardness is obtained by dividing the load by the surface area of the indentation.
Since the indentation is larger than in other hardness tests, it is possible to measure the average hardness of the test material, making it suitable for materials that are not uniform in hardness.
About diamond dressers & types
Diamond dressers
The diamond dresser is a diamond tool used for truing/dressing to restore the sharpness of general grinding wheels and diamond/CBN wheels by correcting dullness, clogging, and peripheral unevenness, or used for forming.
Diamond forming dresser
Diamond forming dresser is made by polishing the diamond at the tip into a roof or wedge shape. The diamond part is polished and formed and is very vulnerable to impact. If the diamond is mounted on the jig in an inclined position, the diamond will be shocked and may be damaged, so it must be mounted correctly.
The depth of cut should be kept within 0.02 mm if possible, and the feed speed should be within 250 mm/min to reduce the risk of damage on the diamond, although it is related to the surface roughness. Always apply cooling water when using the tool. Especially in the case of plastering, the forming distance is long and heat is generated easily, which accelerates the wear of the diamond and shortens its life.
It is used for angular grinding, stepped cylindrical grinding, screw grinding, and gear grinding.
Single-point diamond dresser
The single-point diamond dresser has a diamond with a protruding edge at the tip.
The approximate size of the diamond for the dresser is determined by the specifications (abrasive grain type, grain size, binding degree, and binder) of the grinding wheel to be dressed and the wheel dimensions (diameter and width).
The depth of cut should be 0.015 mm or less for finishing dressings and 0.04 mm or less for rough dressings, and large cuts at one time should be avoided if possible.
Approximate diameter and width of grinding wheel and reference size of diamond
Wheel diameter (mm) |
Wheel width (mm) |
Diamond size |
---|---|---|
Φ150 > | 25 > | 1/3 ~ 1/4 ct |
Φ150 ~ Φ300 | 25 | 3/4 ~ 1 ct |
Φ300 ~ Φ450 | 25 ~ 40 | 1 ~ 1.5 ct |
Φ450 ~ Φ600 | 50 ~ 100 | 1.75 ~ 2 ct |
Φ600 < | 2 ct < |
Multi-point diamond dresser
The multi-point diamond dresser has multiple fixed diamonds.
The type with two or more diamonds evenly spaced and embedded in a single layer on the surface is called a single-layer multi-point dresser, while the type with multiple layers is called a multi-layer, multi-point dresser. Compared to a single-point dresser, the multi-point dresser lasts longer because the load on each diamond can be reduced.
Diamond impregnated dresser
The diamond impregnated dresser is made by mixing and sintering diamond abrasive grains and wear-resistant metal powders, and then attaching a hardened tip of several shape and size to the shank.
The resistance during dressing is distributed among many diamond grains, suppressing wear of the dresser and achieving stable dressing. The types of this dresser are classified by shank shape, diamond grain size, and tip shape.
Indication of spec. of impregnated dressers
of impregnated dressers
Example in case of 2B4A7
-
2
Diamond part
dimension -
B
Diamond
part shape -
4
Grain
size -
A
Shank
shape -
7
Shank
diameter
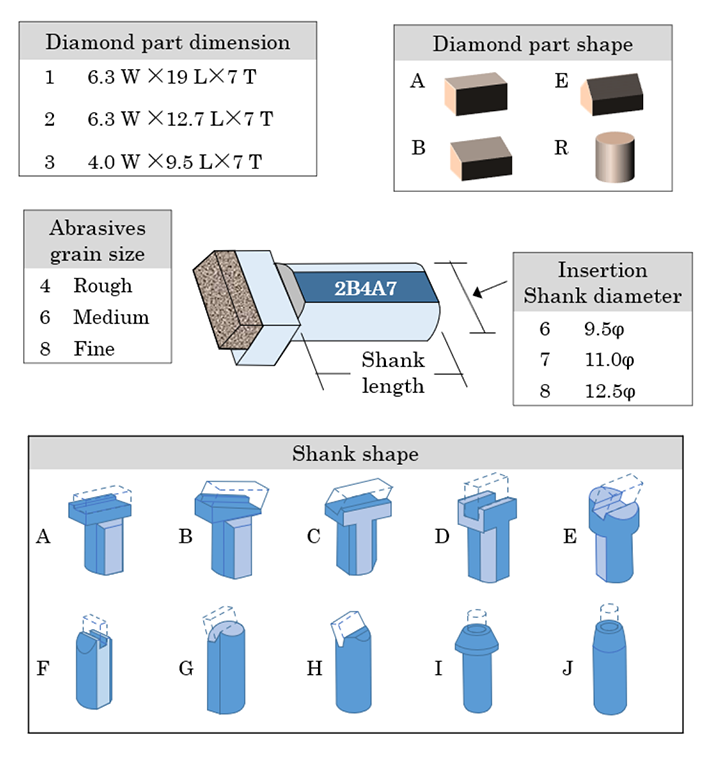