What is Quartz Glass? Characteristics of quartz glass and key points for high efficiency processing
Quartz glass is a high-purity glass containing 99.99% SiO2 [silicon dioxide], the primary component of glass. In comparison to regular glass, quartz glass exhibits superior light transmittance, corrosion resistance, and heat resistance. It finds widespread use in industrial applications such as semiconductor manufacturing processes and optical components.
This article highlights key aspects of the high efficiency processing in grinding of quartz glass, a material that has seen increasing use in recent years.
What is Quartz Glass? Characteristics of quartz and key points of high efficiency processing in grinding
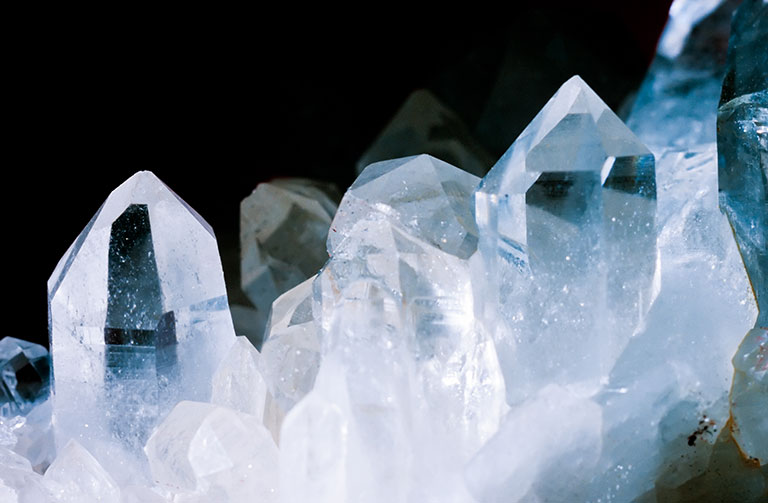
Quartz has various characteristics, including chemical stability, heat resistance, light transmittance, and electrical insulation.
Particularly in semiconductor manufacturing equipment, high-purity quartz glass is required for various processes such as heat treatment film formation, etching, exposure, and wafer cleaning, making it an indispensable material for high-quality semiconductor manufacturing.
In the medical field, quartz glass serves as a crucial component due to its ability to not absorb ultraviolet and infrared rays. It is also employed as a micro flow channel for experiments, making it an essential material in our daily lives. In recent years, the demand for quartz glass has been increasing due to the sophistication and miniaturization of semiconductor devices, driving the need for more precise quartz glass processing.
At processing sites, to enhance the efficiency of processing increasingly complex shapes in quartz glass, there is a growing trend of using "vertical machining centers" equipped with diamond wheels and shafts.
What is quartz glass?
Quartz glass (fused quartz) is a glass consisting of almost pure silica (SiO2). It is also called fused quartz, fused silica, or silica glass. It exhibits outstanding corrosion resistance, heat resistance, and high transparency. It is widely used for physical and chemical applications such as beakers and flasks, as well as serving as a material for optical fibers.References: Wikipedia
Challenges in machining efficiency in quartz glass processing
Quartz glass is known as being a challenging material with poor machinability. During the grinding process, issues such as abrasive grains (diamond) wear and clogging caused by grinding sludge have resulted in low machining efficiency.
Quartz glass, being a hard and brittle material, is prone to chipping, unless the depth of cut per wheel revolution (1 pass) is reduced and the optimum feed rate and cutting speed are determined. Large chipping leads to cracking and machining defects.
[Subject point]
- How to improve the grinding efficiency while reducing chipping of quartz glass
Key points for high efficiency quartz glass grinding
In order to achieve high efficiency grinding of quartz-glass (10mm cutting /1Pass), we conducted evaluation tests using grinding wheels (wheel with shafts) with 6 patterns.
To achieve high-efficiency machining, we investigated the optimal combination of abrasive grain type, bond strength, and concentration (density of abrasive grains) focusing on "grinding resistance" and "maximum chipping size."
〈Evaluation Test Combinations (6 Patterns)〉
Specifications | Abrasive grain type | Concentration | Metal bond | |
---|---|---|---|---|
① | M140 | Abrasive grain A *Current product | High | A (standard) |
② | M140-2 | Abrasive grain B (medium strength) | High | B (high strength) |
③ | M140-3 | Abrasive grain C (high strength) | High | B (high strength) |
④ | M140-4 | Abrasive grain C (high strength) | Low | A (standard) |
⑤ | M140-5 | Abrasive grain B (medium strength) | Low | B (high strength) |
⑥ | M140-6 | Abrasive grain C (high strength) | Low | B (high strength) |
Abrasive grain image |
![]() Abrasive Grains A (current product) |
![]() Abrasive Grain B |
![]() Abrasive Grain C |
---|---|---|---|
Abrasive grain strength | Low strength | Medium strength | High strength |
Abrasive grain shape | Semi-blocky | Semi-blocky | Blocky |
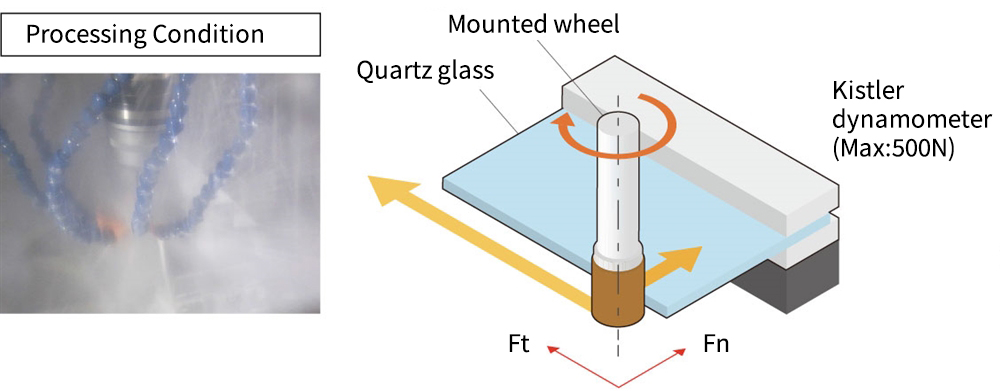
〈Evaluation Conditions〉
- Quartz-glass material dimensions: 100L×50W×5T
- Mounting method: Clamp with special jig
- Processing method: Down cut
- Tool speed: 11,000 rev/min
- Feed speed :200 mm/min
- Cutting depth: 10mm/Pass
- Coolant: Moresco BS-1 Soluble Type (80-fold dilution)
- Coolant volume: 50L/min (6 nozzles)
Evaluation tests revealed that high efficiency grinding (10mm cutting /1Pass) of quartz glass can be achieved by setting high abrasive grain strength and low concentration of grinding wheel (density of abrasive grains) while paying attention to the size of chipping.
This is because the mechanical property of quartz glass, K1C (fracture toughness value), is lower than the hardness of the material, and the hard diamond grain generates and propagates cracks on the surface layer of the material, making it easier to cut.
[Solution Point]
- High efficiency processing of quartz glass is achieved by setting higher abrasive grain strength and bond strength, and low concentration of grinding wheel.
Comparison of grinding resistance
High abrasive grain strength and low grinding wheel concentration (concentration 25) specifications resulted in lower grinding resistance. The lower the grinding resistance, the higher the cutting depth, and the more efficient grinding per wheel revolution (1Pass) can be realized.
On the other hand, since quartz glass chipping increases, attention should be paid to the selection of the abrasive grain size to avoid cracking during processing.
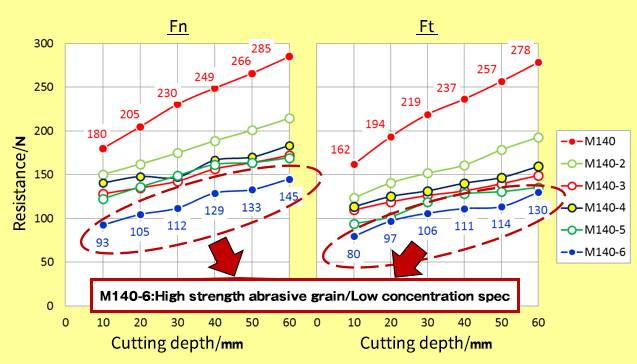
Concerning the size of chipping
Higher abrasive grain strength and higher concentration of the grinding wheel (concentration 45), lead to the smaller chipping of the quartz glass. The smaller the chipping, the higher the grinding accuracy and higher quality processing is achieved.
On the other hand, since the grinding resistance is high, it is important to balance grinding efficiency.
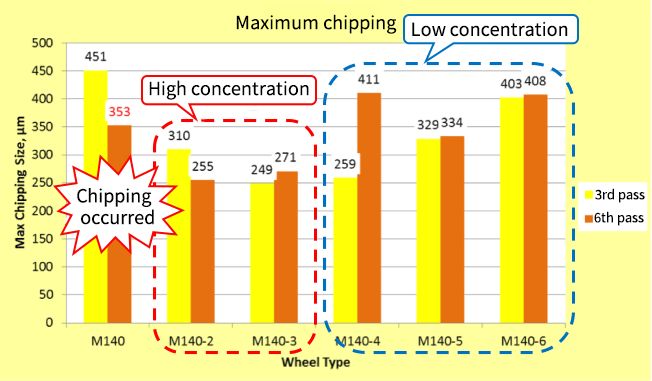
〈Conditional observation of maximum chipping〉
②M140-2, ③M140-3 tend to reduce large-scale chipping.
The high concentration of diamond abrasive grains reduces the stress applied to each single grain resulting in an apparent shallower depth of cut.
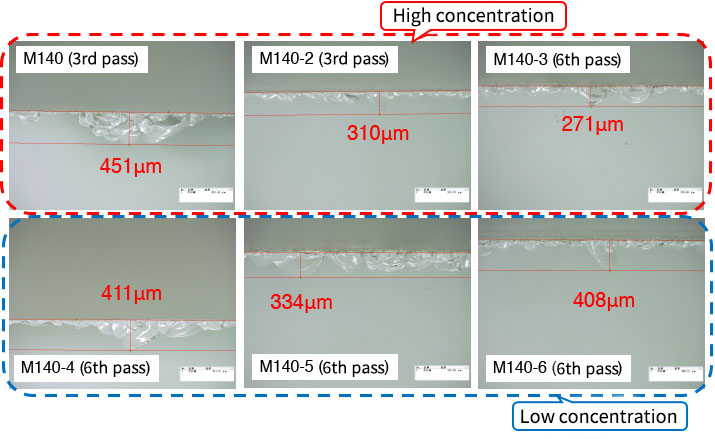
Summary of Efficient Grinding of Quartz Glass
Tokyo Diamond Tool Works has a proven track record in diamond wheel /CBN wheels that are ideal for grinding quartz glass, as well as silicon carbide (SiC), aluminum nitride (AIN), silicon nitride (Si3N4, and other fine ceramics.
If you have any questions about quartz glass grinding or tool selection, please contact Tokyo Diamond Tool Works.