What are the Diamond Wheels? Useful basic knowledge for Diamond Wheels
Diamond wheels are grinding wheels which use diamond abrasive grains as cutting edges. It is called a superabrasive wheels in the sense that it is distinguished from grinding wheels which use general abrasive grains such as SG, WA, GC. And grinding wheels which use diamond abrasive grains are called diamond wheels. Because of the use of hard diamonds as cutting edges, they are increasingly used in semiconductor materials such as silicone and SiC, as well as in functional ceramics.
In this article, titled "What are the diamond wheels?", and we have summarized the basics of diamond wheels, precautions, and tips for using them, and other basic content about diamond wheels.
This article is recommended for young engineers and young sales staff who handle tools.
- What is diamond?
- Use of “diamond wheels” and “CBN wheels”
- The difference between diamond wheels and general grinding wheels?
- About grinding with diamond wheels
- Components of diamond wheels
- Types of diamond wheels
- Diamond wheels specification display
- Applications of diamond wheels
- Cautions and tips for using diamond wheels、コツ
What is diamond?
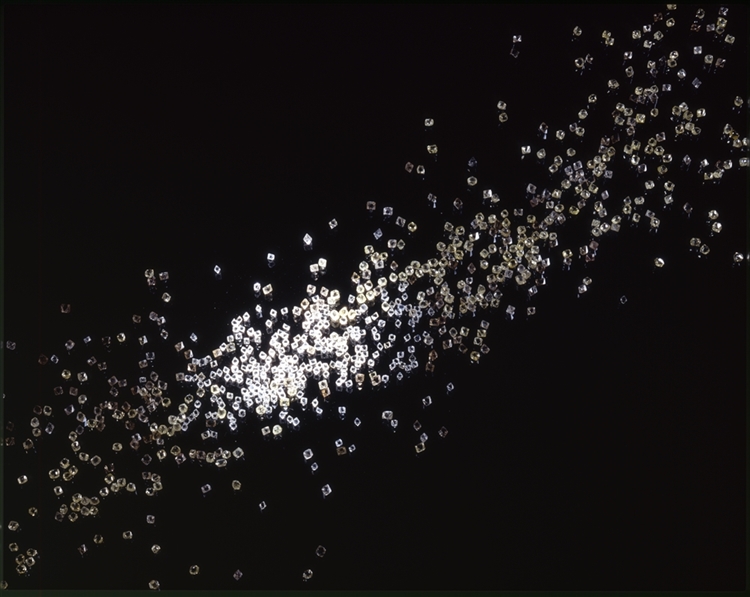
Diamond is the hardest material on Earth. Although it is generally associated with jewelry, it is also widely used as a tool material due to its hardness. The chemical composition of diamond is carbon. It has a diamond structure and hard characteristics.
Characteristics of diamonds
- Hardness: very hard material
- Thermal conductivity: high thermal conductivity reduces temperature rise during machining
- Vulnerable to high temperatures: oxidizes between 600℃ and 700℃
- Limited compatibility with iron: CBN is preferred for iron-based materials due to reduced wear
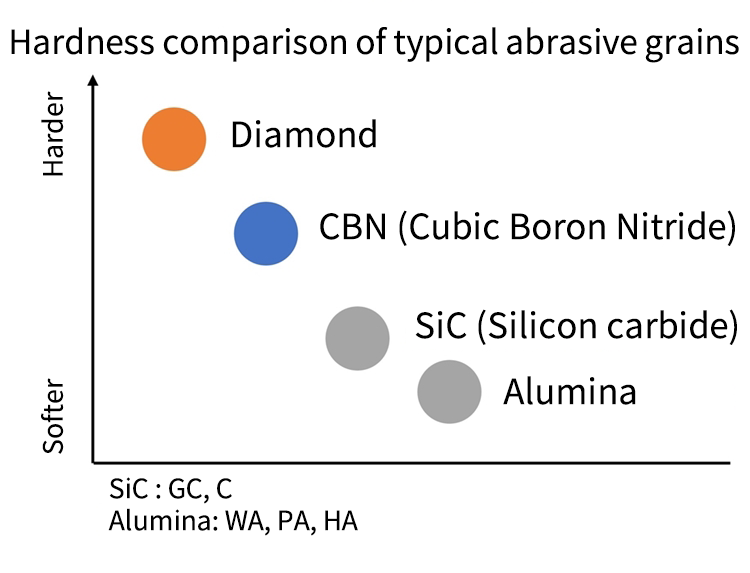
Diamond:
Diamond is a solid form of the element carbon with its atoms arranged in a crystal structure called diamond cubic. Another solid form of carbon known as graphite is the chemically stable form of carbon at room temperature and pressure, but diamond is metastable and converts to it at a negligible rate under those conditions. Diamond has the highest hardness and thermal conductivity of any natural material, properties that are used in major industrial applications such as cutting and polishing tools.References: Wikipedia
Use of “Diamond wheels” and “CBN wheels”
Diamond wheels utilize diamond grains as cutting edges, ideal for grinding "hard materials" challenging for general grinding wheels. However, diamond wheels are not suitable for grinding ferrous materials because are heat-sensitive and chemically wear when grinding iron. CBN (cubic Bron Nitride) wheels are heat resistant and preferred for efficient processing of ferrous materials.
◎Detailed information on CBN wheels is available in the section "Types and Features of CBN Wheels."
What is the difference between diamond wheels and general grinding wheels?
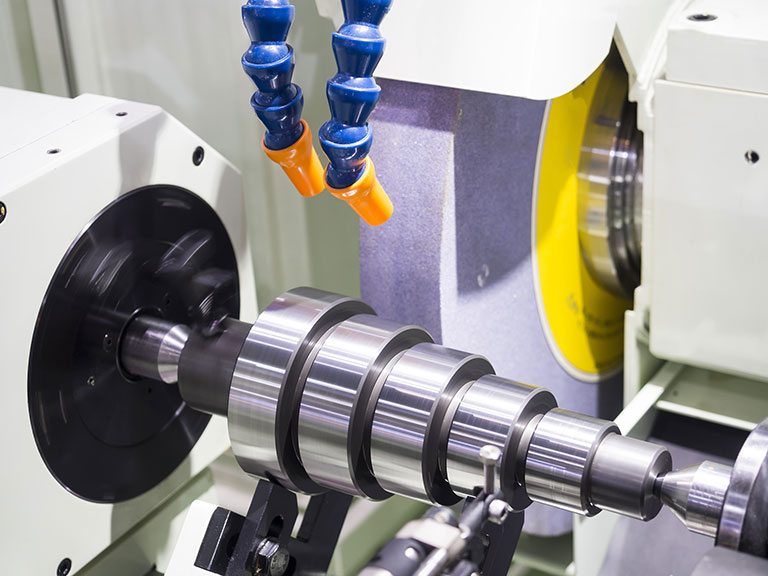
The distinction lies in the grains (abrasive grains) that make up the cutting edge, leading to different designations.
Grinding wheels utilizing diamond or CBN abrasive grains are termed "super-abrasive wheels." This categorization distinguishes them from general grinding wheels, which employ SiC or alumina-based abrasive grains.
Diamond/CBN wheels consist of a diamond/CBN abrasive layer (abrasive grain layer) bonded to a metallic substrate, known as a base metal. In contrast, most general-purpose grinding wheels are formed solely with an abrasive grain layer.
About grinding with diamond wheels
Grinding involves material removal using fixed abrasive grains, present in grindstones and wheels bound by various bonds.
In contrast to cutting with tools like cutting tools, drills and end mills, grinding with a diamond wheel utilizes the diamond grain as the cutting edge.
The diamond wheels are therefore a rotary tool with a number of randomly arranged cutting edges at obtuse angles. A distinct layer (abrasive layer) contains abrasive grains, allowing new diamond grains to be exposed continuously even as the surface diamond wears.
Characteristics of grinding process
- Suitable for machining hard workpieces (many cutting edges and obtuse cutting edges)
- Long tool life (many cutting edges)
- Suitable for the surface grinding of the workpiece (multitude of randomly arranged cutting edges)
- Suitable for high-precision machining (cutting edges with minute abrasive grains)
◎More information on the grinding process is available in "Reference Information on Grinding Tools".
Components of diamond wheels
The diamond wheel consists of three elements: abrasive grains, binder, and pores. Within these, abrasive grains and binder are divided into five factors.
Components of a diamond wheel
Diamond wheel
- 1. Abrasive Grain (Cutting edge)
- Ⅰ type (Abrasive grain type)
- Ⅱ structure (Volume fraction of abrasive grains)
- Ⅲ grain size (Size of abrasive grains)
- 2. Binding material (To hold the cutting Edge)
- Ⅳ type (Bond type)
- Ⅴ binding degree (Hardness of bond)
- 3. Pores (Chip removal, cooling)
General names for diamond wheels
A diamond wheel is created by binding an abrasive grain layer containing diamond abrasive grains to a base, typically using aluminum alloy or iron.
There are different product names for different applications, such as “Straight wheel” – primary the outer circumference is used, “Cup wheel” – mainly the end face is used, and “Mounted wheel”, which has an abrasive grain layer at the tip of the shaft.
Types of diamond wheel
Diamond wheels are broadly classified by the type of bond among the three elements that make up the wheel. Each bond type has distinct features and usage.
◎The explanations of each bond type are introduced in "Reference Information on Grinding Tools".
Diamond resin bond wheel
Diamond resin bond wheels are wheels that use resin as a bond, indicated by the symbol "B."
- Good surface roughness can be obtained due to the appropriate elasticity.
- Easy to drop off the abrasive grains during the processing, and the other grains show up instead which keep the wheel grinding sharp.
- Limited heat resistance compared to other bonds, resulting in a shorter lifespan.
- Widely applied in various applications.
Diamond metal bond wheels
Diamond metal bond wheels are wheels that use metal as a binder (bond), indicated by the symbol "M."
- Bond has high wear resistance and abrasive grain retention, resulting in long life.
- High thermal conductivity and good heat dissipation, reducing thermal deterioration of abrasive grains during grinding.
- Lack of elasticity causes abrasive grains to bite into the workpiece well. On the other hand, deteriorating surface roughness.
- Suitable for processing hard and brittle materials, promoting chip removal and maintaining sharpness persistence.
Diamond vitrified bond wheels
Diamond vitrified bond wheels are ceramic wheels that use ceramic as a binder (bond), indicated by the symbol "V."
- Good sharpness
- Provides good balance between lifespan and grinding durability.
- Due to the brittle characteristics, its uses are limited. Difficult to handle.
- Easy truing (molding) due to brittleness, enabling shaping of the forming wheel.
- Poor thermal conductivity, leading to heat accumulation; however, it forms pores easily compared to other bonds which promotes chip removal and can provide a cooling effect.
Diamond electroplated wheels
This wheel has abrasive grains plated to a metal base, and one diamond layer is formed on the surface. Indicated by the symbol "P."
- Highest retention force of abrasive grains, larger protrusion compared to other bonds, and excellent sharpness.
- Good bite of abrasive grains, but surface roughness may suffer.
- Easy manufacturing of complex shapes depending on the shape of the base metal.
- Re-electroplated (repairing) is possible by peeling off the plating and plating the abrasive grains again.
- Shorter lifespan due to a single diamond layer
There are different types of diamonds for different applications. There are also composite and special bonds with combined characteristics.
Diamond wheels spec indication
SDC | 200 | N | 100 | BDH | 3.0 |
---|---|---|---|---|---|
Type of abrasive grain | Grain size | Binding degree | Concentration | Type of bond | Thickness of abrasive layer(mm) |
Diamond wheels are typically defined by five components known as the "wheel specification." (Note: Some indications may vary based on the manufacturer or product.)
Wheel-specification indications adhere to JIS regulations, yet individual manufacturers often establish their own specifications, incorporating unique know-how elements.
For instance, while JIS specifies the bond type symbol for resin bonds as "B," manufacturers may use their own bond names, such as "BDH" as in here .
Selecting specifications requires a rule of thumb, considering factors like workpiece material, shape, required quality, and machining method. Contact us for assistance!
Applications of diamond wheels
Diamond wheels are used in various industries and have many applications:
Machining of semiconductor materials
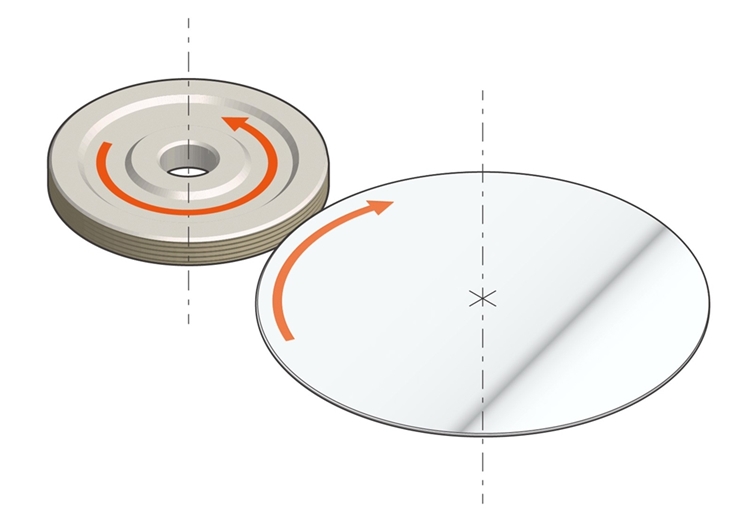
Machining of semiconductor wafers
- Edge grinding of silicon wafers
- Notch grinding of silicon wafer
- Edge grinding of SiC wafers
- Wafer grinding of SiC wafers
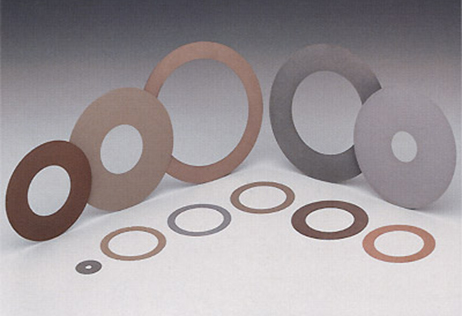
Machining of semiconductor-related materials
- Cutting the package substrate
- Edge grinding of support glass
Machining of semiconductor manufacturing equipment parts
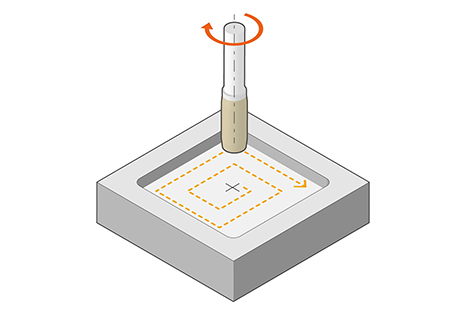
Machining of ceramic and quartz
Machining of automotive parts
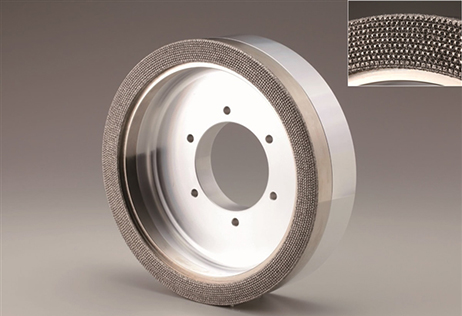
Machining of various automotive parts
- Machining of brake pads
- Edge grinding of the touch panel glass
- Machining of ceramic parts around engines
- Cutting of CFRP and GFRP
Machining of tools
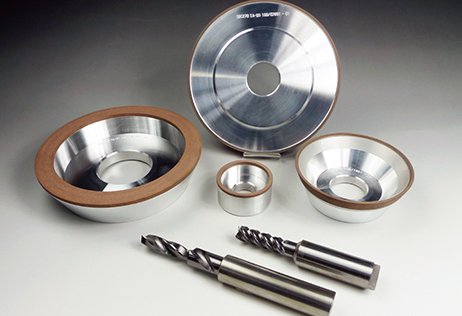
Machining of cutting tools
- Machining of carbide drills, end mills, and other cutting tools
- Machining of PCD and PcBN cutting tools
- Cutting a round bars which is made of carbide alloy
Machining of precision equipment
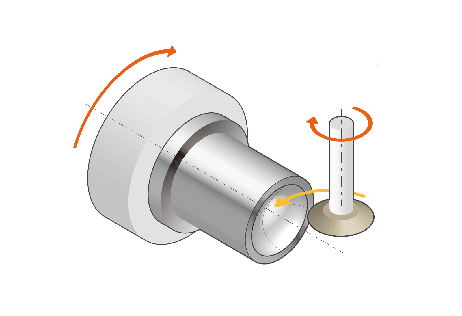
Machining of motor materials and sensor materials
- Machining of magnetic materials such as ferrite and samarium cobalt
- Machining of glass lens molds
Cautions and tips for using diamond wheels
Free documents in the "Diamond Tool Useful Information" provide details on precautions and tips for using diamond wheels.
The materials provide more detailed information than presented in this article and explain the following: