How to prevent chipping in grinding? Causes and improvements in chipping
One of the persistent challenges faced by users of diamond grinding wheels is the occurrence of chipping on the workpiece.
Chipping refers to the presence of small fractures or cracks. The prevalence of concerns related to chipping is due to the fact that the work materials processed with diamond wheels often exhibit both hard and brittle properties. Common brittle materials include glass, ceramics, silicon, and compound semiconductor materials used in the semiconductor industry.
The growth of the semiconductor industry has increased the use of diamond wheels for machining not only semiconductor materials but also quartz glass and ceramics. Furthermore, the required precision for chipping has improved, leading to instances where allowable chipping becomes defective, impacting yield. Consequently, consultations on chipping-related issues are on the rise.
In this article, we will explore why chipping occurs on the work material during grinding with diamond wheels. We will delve into the causes and present key points for improving chipping.
- Challenges of workpiece chipping in grinding
- Mechanism of chipping occurrence in grinding
- How to improve chipping in grinding operations
- How to distinguish between normal and abnormal chipping
- Causes of abnormal chipping and points for improvement
- Cause of abnormal chipping
- Please contact us for improvement of abnormal chipping in the grinding process
Challenges of workpiece chipping in grinding
While "chipping generated on the cutting edge of the tool" is a common issue in cutting, when grinding with a diamond wheel, the concern shifts to "chipping generated on the machined surface of the work material (workpiece)."
Numerous workpieces requiring diamond wheel machining are composed of hard and brittle materials. These brittle materials are prone to scratches and cracks, and if excessive chipping occurs, it can lead to product failure, ultimately lower the yield.
Therefore, in grinding brittle materials, understanding the mechanism of chipping, and estimating the cause of chipping will lead to higher yields.
Workpiece materials prone to chipping
Brittle materials susceptible to chipping encompass a wide range, including ceramics, glass, semiconductor and crystal materials, and various tool materials.
- Ceramics
Aluminum nitride (AlN), Silicon carbide (SiC), Silicon nitride, Boron carbide (B4C), Boron nitride (BN), Alumina ceramics, Cordierite, Clear ceramics, Zirconia ceramics, Porous ceramics, Ferrite magnets, Various magnetic materials, etc.
-
Glass
Quartz glass, Optical glass, Soda-lime glass, Aluminosilicate glass, Borosilicate glass, Fluorite, Neoceram, etc.
-
Semiconductor materials and crystal materials
Silicone, SiC, LT, LN, GaN, GaAs, GaP, Quartz, Optical crystals, Diamond, Sapphire, Jewels and other precious stones
-
Tool material
PCD (diamond-sintered body), PCBN (CBN sintered body), Cemented carbide, Carbon steel, etc.
*Improvement methods for abnormal chipping, a challenge in grinding, are detailed below.*
Mechanism of chipping occurrence in grinding
In practice, chipping is a constant presence during the processing of brittle materials using diamond wheels. This is attributed to the transformation of small diamond grains into cutting edges by the diamond wheel, resulting in the fine crushing and processing of the work material.
While general cutting work in metals (ductility mode) produces continuous thin and long chips, grinding work (brittle fracture mode) generates fine chips, indicating a finely crushed material.
At the machining point of the work material, minute brittle fracture occurs during grinding, and typically, the machined surface consists of a fracture surface containing brittle fracture cracks (chipping).
Brittle fracture:
Fracture with almost no plastic deformation. The fracture of glass or ceramics is a typical brittle fracture, which is caused by rapid development of cracks.References: The Japan Society of Mechanical Engineers
How to improve chipping in grinding operations
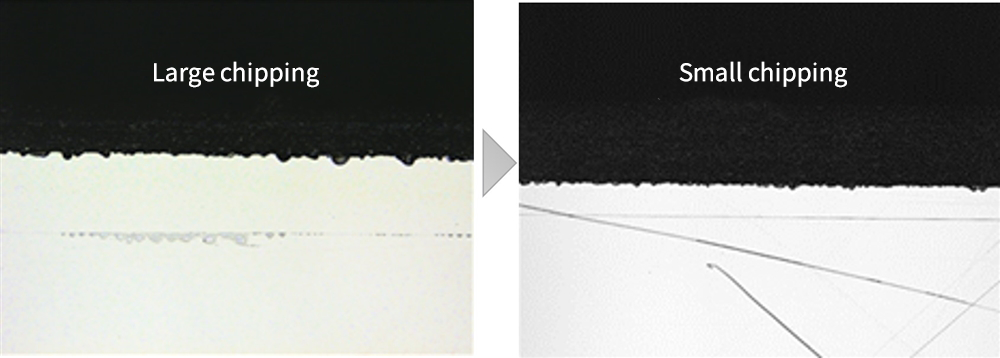
Chipping is an inherent occurrence in the grinding of brittle materials. Therefore, the focus is on reducing and improving chipping rather than completely eliminating it.
The key lies in interpreting that "chipping is big" rather than framing it as "chipping is emerging." Instead of solely exploring why chipping occurs, understanding why significant chipping occurs becomes crucial for chipping improvement.
During the grinding of brittle materials, chipping arises from the meticulous destruction and processing of the work material. To distinguish problematic chipping from that inherent in the normal grinding process, we assess the "diamond grain size of the grinding wheel" as a reference for typical chipping dimensions.
*Improvement methods for abnormal chipping, a challenge in grinding, are detailed below.*
How to distinguish between normal and abnormal chipping
Identifying the size of the chipping is an important point for improving chipping.
By comparing the size of the generated chipping with the average particle size of the diamond grains in the grinding wheel, assessed through "mesh sizes" and "micron sizes," it can be determined whether the chipping is within the normal range or exhibits abnormal characteristics.
Diamond wheels are categorized by particle size, indicated by "mesh sizes" determined through sieves and "micron sizes" representing fine particles. Using the "Average Particle Size," calculated as the average of these particle sizes, serves as a reference to judge the normality or abnormality of the chipping.
The average particle size (specification of wheel, abrasive grain size) is provided below.
Normal chipping
Normal chipping occurs when the chipping size aligns with the average grain size of the grinding wheel. To reduce the chipping size, consider switching to a grindstone with a smaller average grain size and finer grains.
The size of the average grain size is also a point when selecting the grain size of the diamond wheel. For machining brittle materials where chipping is a problem, it is necessary to select a diamond wheel with an average grain size smaller than the allowable chipping size.
Abnormal chipping
When the chipping size exceeds the average particle size, it indicates the occurrence of abnormal chipping (typically considered a range of variation when exceeding several μm).
If abnormal chipping occurs, refining the diamond wheel's grain size will not improve chipping. A finer diamond grain reduces the sharpness of the diamond. This increases resistance, which can lead to vibration and adverse effects.
Causes of abnormal chipping and points for improvement
The root cause of abnormal chipping lies in impacts resulting from vibrations. Brittle materials are generally known to be vulnerable to impact and vulnerable to scratching. In grinding, normal chipping is always caused by an impact during the grinding process. However, abnormal chipping is caused by unusual impacts on the workpiece due to vibrations exceeding the norm in grinding operations.
When abnormal chipping occurs, the initial steps involve checking two critical points: "grinding wheel runout" and "dressing."
Check the runout of the grinding wheel.
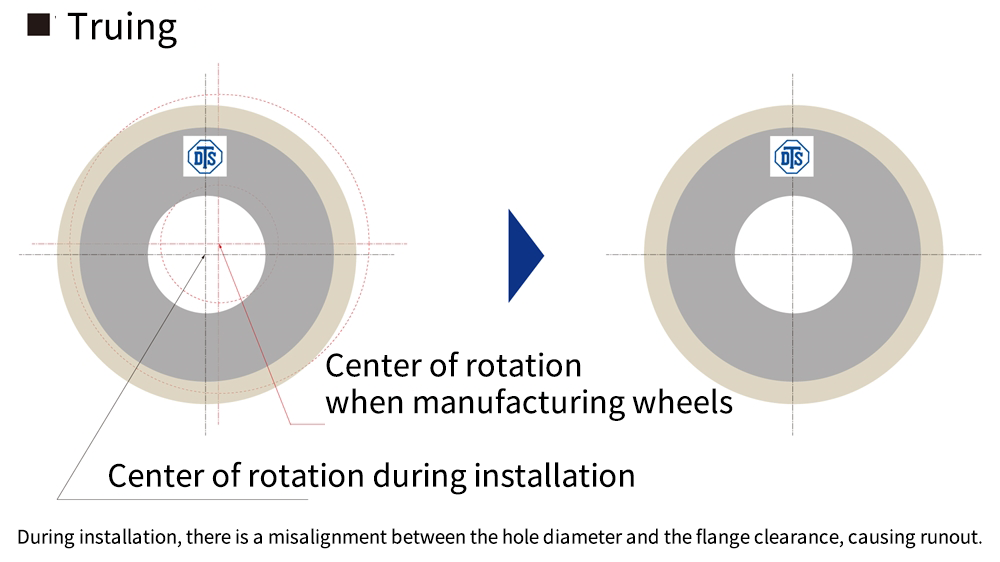
If abnormal chipping occurs, first check the grinding wheel for runout by using a dial gauge or a similar tool on the machine.
If grinding is performed with runout, the grinding wheel intermittently impacts the workpiece, generating undesirable impacts.
When installing a grinding wheel to the grinding machine, runout can occur due to center misalignment. First, perform run out due to truing and dressing on the machine.
Dressing (sharpening) is performed.
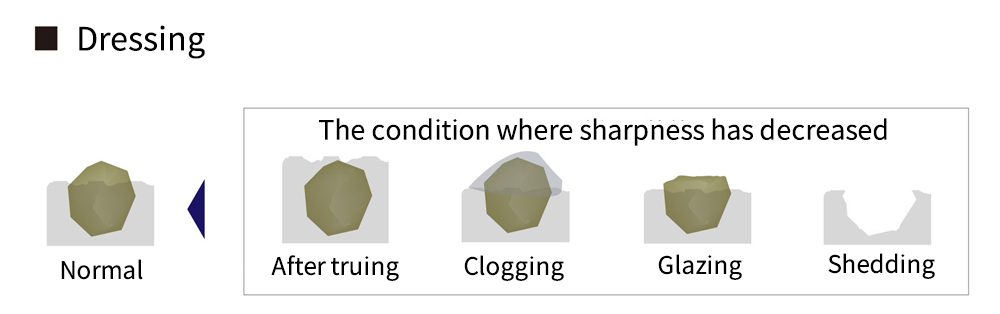
At the next step, please check the grinding surface of the wheel for defects by dressing (sharpening).
Diamond wheels experience reduced sharpness through use, leading to conditions like clogging, glazing, or shedding. Low sharpness can result in impacts due to vibrations.
If dressing resolves abnormal chipping, the cause is likely the diamond wheel's sharpness. Please implement measures such as "periodic dressing" and "adjusting machining conditions to enhance sharpness."Cause of abnormal chipping.
If dressing fails to resolve abnormal chipping issues, investigate potential causes systematically.
Other possible causes of abnormal chipping include the following:
- Effect of Chips and Fallen Abrasive Grains:
Chips and abrasive grains can impact machining when caught during grinding, often observed in abnormal chipping with specific regularities like streaks.
- Coolant Problem:
Issues with coolant can lead to sudden abnormal chipping. Proper coolant is crucial for chip discharge and heat suppression.
- Lack of Sharpness:
Insufficient sharpness results in vibration and applied impact.
- Machining Conditions:
Check grinding wheel peripheral speed, cutting depth, and cutting speed. If the peripheral speed of the grinding wheel is high, the abrasive grains will not properly work to the workpiece, causing a decrease in sharpness.
- Processing Method:
Try the processing by down cutting.
Devise tool paths and machining methods.
Vibrations in the workpiece can also be suppressed by devising ways to hold the workpiece.
Please contact us to improve abnormal chipping during grinding
There are many types of grinding processes with diamond wheels, including surface grinding, cylindrical grinding, internal grinding, centerless grinding, cutting, grooving, and machining with a grinding center, as well as many types of work materials. Depending on the machining methods, the factors that may cause chipping also vary. Since it is difficult to respond to all machining cases uniformly, the measures must be taken in accordance with each case.
Tokyo Diamond Tool Mfg not only assists in selecting and modifying grinding wheel specifications but also provides consultation on machining conditions, truing and dressing tools, grinding fluid, and various other aspects.