What are CBN wheels? Types and characteristics of CBN Wheels. Summary of machining examples
CBN is an acronym for Cubic Boron Nitride (CBN), is a compound that is second only to diamond in terms of hardness. CBN wheels are high-efficient, long-life, super-abrasive wheels.
In recent years, demand for CBN wheels has been increasing due to the growing need for grinding heat-resistant alloys for the aerospace industry and high-speed steel for molds.
In this article, we will introduce the distinction between diamond wheels and CBN wheels based on materials, types of CBN wheels, and examples of CBN wheel machining.
Super-abrasive wheels (diamond/ CBN)
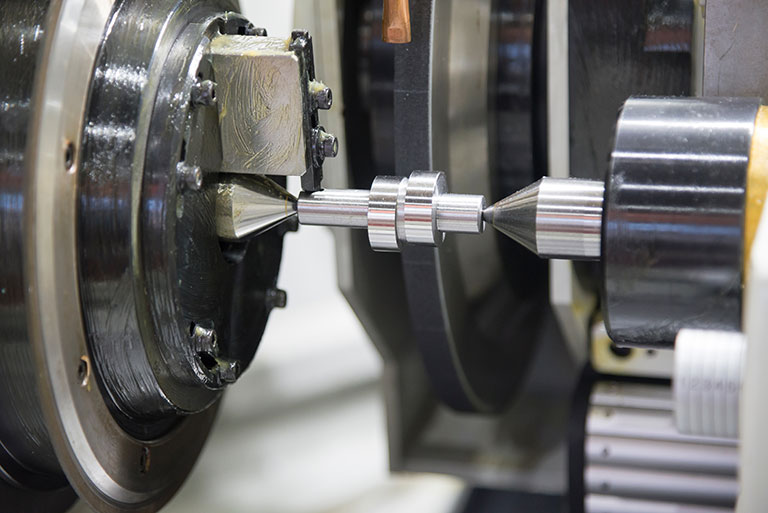
A grinding wheel is a rotary tool that is rapidly rotated to process a large number of cutting edges, formed by the hard fine particles known as abrasive grains embedded in the grinding wheel. This tool is used to cut and remove material, and unlike conventional cutting rotary tools, it features a very high number of cutting edges arranged randomly. Due to this configuration, it is well-suited for achieving a fine finish, has a long tool life and is suitable for high-precision machining.
Furthermore, it differs from rotary cutting tools in that it contains a layer of abrasive grains known as the abrasive layer with a certain thickness. Even as the tool wear progresses, the tool can continue to be used for the thickness of the abrasive layer.
Grinding wheels come in two main types: “General whetstones” that use abrasive grains such as SiC (silicon carbide) or alumina, and “Super abrasive wheels” that use abrasive grains like diamond or CBN (cubic boron nitride). These are primary mounted on machines such as surface grinders, polishing machines, and automated machinery for various grinding applications.
(Generally, when referred to as "wheel" it specifically denotes super abrasive wheels.)
Super abrasive wheels, while more expensive compared to general whetstones, offer advantages in terms of tool life and precision. Choosing between them based on the application is a key factor in enhancing productivity.
Use different “Diamond wheels” and “CBN wheels”
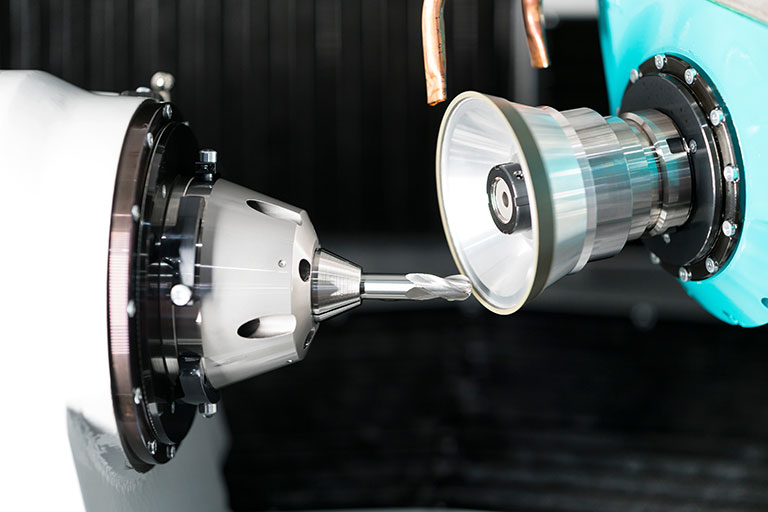
There are two types of super abrasive wheels: "Diamond wheels", which use diamond and “CBN wheels,” which use CBN. Diamond wheels utilize the hardest material on Earth, where carbon atoms are covalently bonded. They are employed for grinding “hard materials” that are challenging to grind with conventional abrasives. However, diamond has low heat stability and chemically react with iron, making it unsuitable for grinding iron-based materials. Therefore, CBN wheels are used for such applications.
CBN stands for Cubic Boron Nitride, a compound that boasts hardness second only to diamond. Compared to diamond, CBN has higher thermal stability and is less likely to react with iron, making it suitable for grinding iron-based materials.
CBN:
Cubic Boron Nitride (CBN), the simplest group III-V compound composed of boron and nitrogen. It is an artificially produced material not found in nature and it has a crystal-structure similar to diamond.References: National Institute for Materials Science
Use different “Diamond wheels” and “CBN wheels”, depending on work materials
Generally, diamond wheels are used for non-ferrous metals, while CBN wheels are used for ferrous metals.
CBN wheels are second only to diamond in hardness exhibiting higher hardness and lower wear compared to regular abrasives (or abrasives grains) making them suitable for efficient machining of iron-based materials that diamond may struggle with. Typically, CBN is more expensive than diamond, so diamond is primary used in areas where it is effective.
Additionally, in machining areas where abrasive grains coarser than #40 are used, CBN is not common, and diamond is preferred. Conversely, in areas using fine abrasive grains, CBN is not often used, and micron sized CBN, finer than #400, is not commonly used.
Material suitable for Diamond wheels | Materials suitable for Diamond/CBN wheels | Materials suitable for CBN wheels |
---|---|---|
|
|
|
Differentiation between CBN wheels and general whetstones?
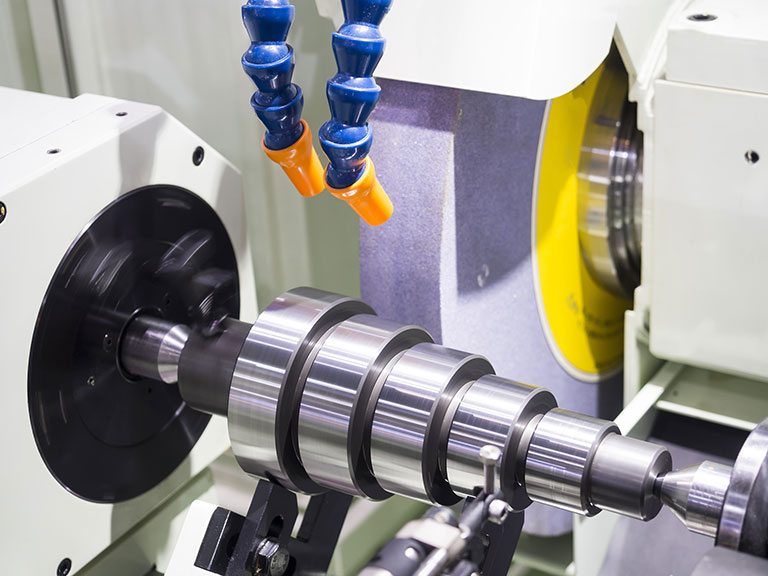
Most materials that can be ground with CBN wheels can also be ground with general whetstones. However, from the perspective of machining efficiency and tool life, there are many cases where CBN wheels are replaced with general whetstones.
The machining accuracy of grinding wheels depends on the accuracy of the machine equipment itself, but the use of CBN wheels, which are resistant to wear, can make it easier to achieve precision.
Comparison between CBN wheels and general whetstones
CBN wheel | General whetstones | |
---|---|---|
Life | Durable with low wear | Prone to wear with a shorter life |
Unit price | High cost | Low cost |
Precision | Easier to achieve precision | Challenging to achieve precision |
◎Key points for selecting CBN wheels
- Although CBN wheels come with higher unit price, they significantly reduce running costs by offering a longer life and reducing the frequency of wheel replacements.
- Due to low tool wear during processing compared to general whetstones, CBN wheels enable high-precision machining even in application with stringent accuracy requirements.
- The low tool wear of CBN wheels is particularly advantageous in the machining of the precision-demanding items, reducing the frequency of correcting worn tool dimensions.
- As used general whetstones become industrial waste, replacing them with longer-lasting CBN wheels contributes to cost reduction in waste disposal and aligns with efforts towards achieving SDGs (Sustainable Development Goals, specifically Goal 12: “Responsible Consumption and Production”).
Types and characteristics of CBN wheels
CBN wheels are broadly categorized into four types based on the using bond:
CBN vitrified bond wheels
CBN vitrified bond wheels are those in which abrasive grains are bonded with a glassy (inorganic material) binder. This type of wheels demonstrate exceptional sharpness and self-sharpening capabilities under high-load conditions, thanks to their hard and brittle characteristics. Their porous structure enhances chip discharge, and their relatively straightforward molding and truing processes contribute to their overall performance.
CBN resin bond wheels
CBN resin bond wheels are wheels which abrasive grains are bonded with a resin (thermosetting resin) binder. This type of wheels offers high sharpness and are ideal for high-precision machining like mirror finishing. They are versatile and applicable to a wide range of materials and grinding methods. Truing and dressing are relatively easy, and it makes this bond user-friendly.
CBN metal bond wheels
CBN metal bond wheels are wheels where abrasive grains are bonded with metal powder under strict temperature and atmosphere control. They have high retention force of abrasive grains that provides excellent heat dissipation, heat resistance, and wear resistance. Their shape retention is higher compared to resin bonds and other materials, making it suitable for shaping processes.
CBN electroplated wheels
CBN electroplated wheels are grinding wheels which CBN abrasive grains are adhered to the metal-base by plating. Unlike other bonds, they have a single layer of cutting edges, resulting in a shorter life compared to other bonds. However, they offer high sharpness and are relatively inexpensive with short lead times. With protruding abrasive grains larger than that the other bonds, this type of wheels brings a higher cutting ability. They are suitable for complex shaping processes as they can be produced relatively easy compared to other bonds. Additionally, re-electroplating is possible by detaching the plating layer and re-electroplating the abrasive particles.
Machining examples with CBN wheels
Tokyo Diamond Tools offers a wide range of grinding tools from the production of various diamond tools to the customization of complex-shaped vitrified wheels, enabling high-efficiency grinding processes.
Among them we would like to introduce machining examples using CBN wheels (resin bonds, metal bonds, electroplated).
Machining of mechanical components with CBN wheels
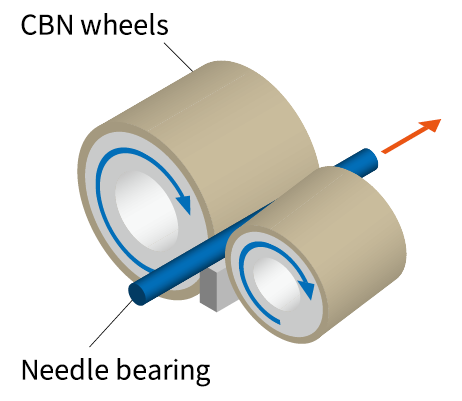
Machining of Needle bearings with CBN Wheels
Long-duration machining of the ‘rollers’ of high-hardness needle bearing is achieved with CBN resin centerless wheels. Balancing the wheel grain size and specifications of the wheel allows for a combination of grinding durability and finishing precision.
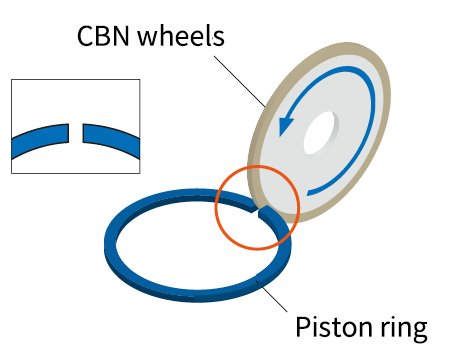
Machining of piston ring with CBN wheels
Efficient processing of piston rings with surface treatment is achieved with using CBN electroplated wheels.
Furthermore, the ‘DEX Duo Compound Electroplated Wheel,’ boasting even higher shape retention, can reduce shape distortion by approximately 1/3 compared to conventional electroplated wheels.
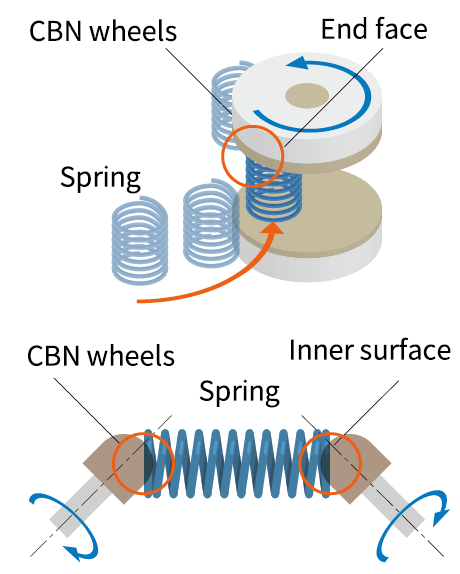
Machining of spring end faces and inner chamfers with CBN wheels
Time reduction in processing thick wire diameter spring end faces is achieved with high-durability CBN electroplated wheels. With high shape retention, it is also ideal for chamfering the inner surface of springs.
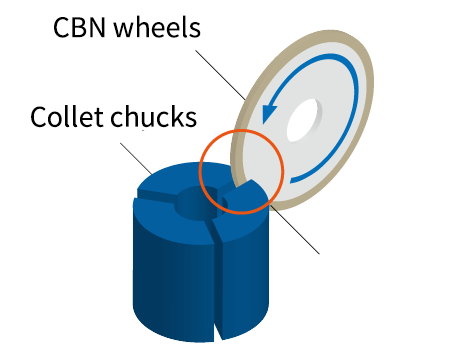
Machining of collet chucks with CBN wheels
CBN resin wheels enable grinding of collet chucks. High shape retention allows for stable processing with maintained accuracy.
Machining of neodymium magnets with CBN wheels
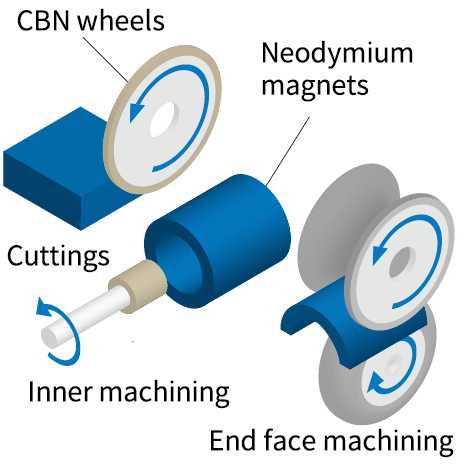
Efficient processing of neodymium magnets is achieved with CBN resin bonded wheels. Optimization of abrasive grains reduces chipping of the workpiece, while maintaining a moderate self-sharpening ability for sustained sharpness.
Mold machining with CBN wheels
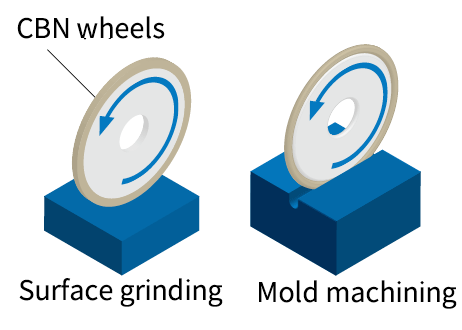
Surface grinding machines and form grinding machines using CBN wheels
CBN resin bond wheels achieve high-precision surface machining, groove cutting, and shaping of molds.
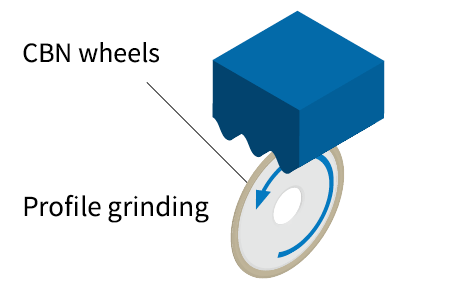
Grinding on profile grinding machines with CBN wheels
CBN metal bond wheels enable high-precision machining of fine molds, punches, and dies.
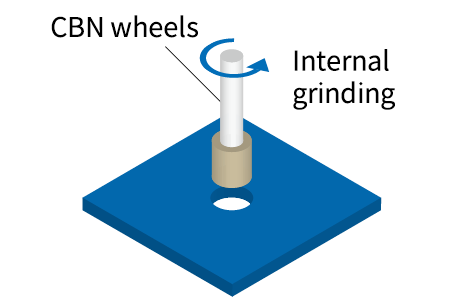
Grinding on jig grinding machines with CBN wheels
CBN electroplated wheels achieve high-precision internal grinding and hole drilling of precision molds.
Tool and blade processing with CBN wheels
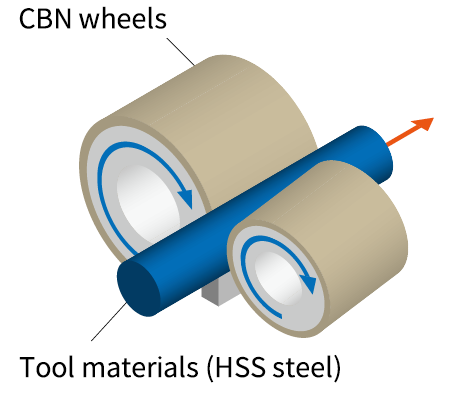
Machining of tool materials with CBN wheels
CBN resin centerless wheels achieve high-efficiency external grinding of round bar tool materials (HSS steel) with long life.
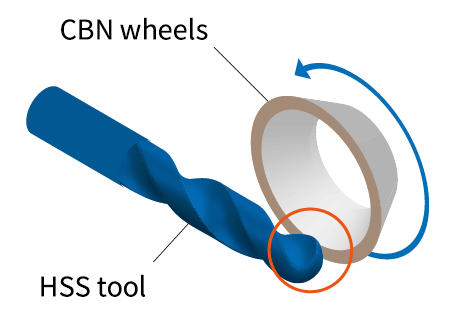
Machining of HSS tools with CBN wheels
CBN metal bond wheels enable stable grinding of HSS tools. By controlling the self-sharpening of abrasive grains, they produce grinding surfaces without grinding burn and waviness.
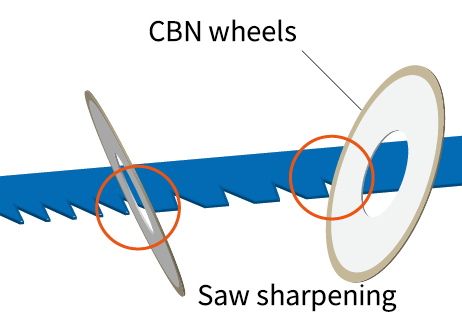
Saw sharpening with CBN wheels
CBN metal bond wheels enable sharpening the saws that are used in woodworking and other applications. High shape retention and long life enables continuous use even with automatic machines using replaceable blades.
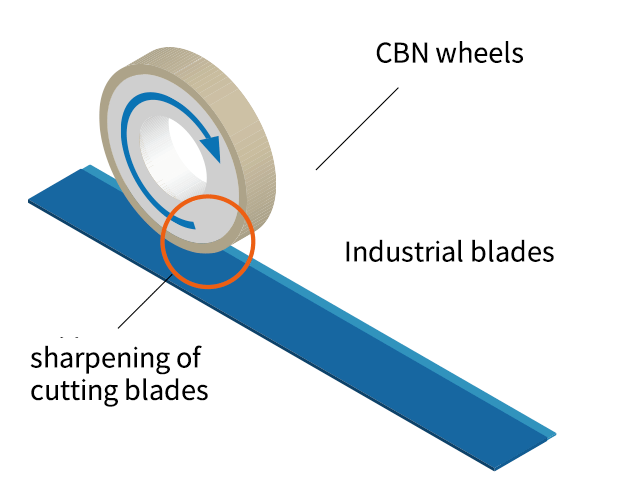
Machining of industrial blades with CBN wheels
CBN resin bond wheels can help achieve the sharpening of cutting blades and slitter blades used for cardboard, printed materials, etc.
It has a long life, so continuous processing is possible even with long or large-area blades.
Summary of CBN Wheels
Tokyo Diamond Tool offers an extensive selection of diamond tools, encompassing CBN resin bond wheels, CBN metal bond wheels, CBN electroplated wheels, and more. We deliver customized grinding wheels tailored to the work material and processing specifications. Custom orders for single wheels are also welcomed.
For machining and processing consultation, as well as assistance in selecting CBN wheels and customizing complex-shaped profile wheels, please feel free to reach out to Tokyo Diamond Tools for additional information.